Quick and Reliable Product Packaging Equipment Repair Service Services to Decrease Downtime
In the affordable landscape of production, the efficiency of packaging procedures pivots on the dependability of machinery. Quick and trustworthy repair work services are essential in mitigating downtime, which can lead to considerable economic losses and functional setbacks.
Relevance of Timely Services
Prompt fixings of product packaging equipments are critical for keeping functional performance and lessening downtime. In the hectic atmosphere of production and packaging, also small malfunctions can result in significant delays and performance losses. Resolving concerns immediately guarantees that devices operate at their optimum capability, thus protecting the flow of procedures.
Additionally, prompt and routine maintenance can protect against the rise of minor problems right into major breakdowns, which often sustain higher fixing expenses and longer downtimes. A proactive strategy to maker repair work not just protects the integrity of the tools however also boosts the general integrity of the assembly line.
Furthermore, timely fixings add to the durability of packaging equipment. Makers that are serviced quickly are less most likely to struggle with excessive damage, enabling organizations to maximize their investments. This is specifically essential in sectors where high-speed packaging is crucial, as the requirement for regular performance is vital.
Advantages of Reliable Company
Reputable company play a critical duty in making sure the smooth operation of packaging equipments. Their expertise not just enhances the performance of repair services yet likewise adds significantly to the durability of tools. Dependable solution carriers are equipped with the technical knowledge and experience required to identify concerns properly and apply effective services rapidly. This minimizes the threat of reoccuring troubles and ensures that machines operate at optimum performance levels.
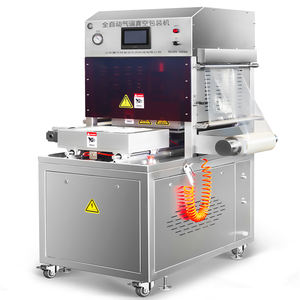
In addition, a trusted solution supplier uses thorough support, including training and guidance for staff on machine operation and maintenance finest techniques. This not only equips staff members but also grows a society of security and performance within the organization. Overall, the advantages of involving trustworthy company extend past instant repair work, positively influencing the entire operational operations of packaging processes.
Usual Product Packaging Device Issues
In the realm of product packaging operations, different concerns can compromise the effectiveness and functionality of devices (packaging machine repair). An additional common problem is imbalance, which can cause jams and unequal product packaging, impacting product top quality and throughput.
Electric problems can likewise interfere with packaging operations. Damaged wiring or malfunctioning sensors might cause erratic device habits, creating delays and increased operational prices. Additionally, software application problems can prevent the machine's programming, causing functional inadequacies.
Irregular product flow is one more critical issue. This can emerge from variants in product form, weight, or read here dimension, which might influence the machine's ability to deal with products precisely. Lastly, inadequate training of operators can exacerbate these problems, as inexperienced employees might not identify very early indications of malfunction or might misuse the devices.
Dealing with these common product packaging equipment concerns immediately is vital to keeping efficiency and guaranteeing a smooth operation. Normal assessments and positive maintenance can significantly minimize these worries, fostering a dependable packaging setting.
Tips for Decreasing Downtime
To lessen downtime in packaging procedures, carrying out a click proactive upkeep method is important. Frequently scheduled upkeep checks can identify possible problems prior to they intensify, making sure devices run successfully. Establishing a routine that consists of lubrication, calibration, and inspection of essential elements can significantly minimize the frequency of unforeseen breakdowns.
Training personnel to run machinery appropriately and recognize very early warning indications of breakdown can likewise play an essential function. Encouraging operators with the understanding to execute basic troubleshooting can protect against minor problems from creating significant delays. Additionally, keeping an efficient stock of important extra components can expedite repair services, as waiting for parts can cause extensive downtime.
Additionally, documenting maker efficiency and upkeep tasks can help identify patterns and frequent problems, permitting targeted treatments. Including advanced monitoring technologies can supply real-time information, allowing anticipating upkeep and lessening the threat of abrupt failings.
Last but not least, cultivating open interaction in between drivers and maintenance teams guarantees that any type of irregularities are quickly reported and dealt with. By taking these positive steps, companies can enhance operational performance and significantly lower downtime in product packaging procedures.
Selecting the Right Repair Work Service
Choosing the appropriate fixing service for product packaging makers is a vital choice that can substantially impact operational performance. Begin by assessing the copyright's experience with your certain type of product packaging equipment.
Following, consider the company's online reputation. Seeking comments from various other services within your sector can provide understandings right into integrity and high quality. Qualifications and partnerships with acknowledged tools manufacturers can likewise show a commitment to excellence.
Furthermore, More hints analyze their response time and accessibility. A company who can use punctual assistance minimizes downtime and keeps manufacturing circulation constant. It's also important to make inquiries concerning warranty and service warranties, which can show the self-confidence the provider has in their work.

Verdict
Finally, the relevance of trusted and quick packaging maker repair work solutions can not be overstated, as they play a crucial function in minimizing downtime and making certain operational performance. By prioritizing prompt repair work and selecting reputable company, companies can properly keep and deal with usual issues efficiency. Implementing positive upkeep practices and buying staff training additional boosts the longevity of packaging equipment. Inevitably, a tactical technique to fix services promotes a much more resistant production environment.
Prompt repairs of packaging machines are critical for preserving functional effectiveness and reducing downtime.Additionally, timely fixings add to the longevity of packaging machinery. On the whole, the benefits of engaging reliable solution providers prolong beyond prompt repair services, favorably affecting the entire functional operations of product packaging procedures.

Comments on “Save Time and Money with Effective Packaging Machine Repair Services”